INTRODUCCIÓN
El presente trabajo tiene como finalidad primordial el incorporar al alumnado a los conocimientos básicos de un taller mecánico estos conocimientos son la columna vertebral de este tales como lo son el torno, fresadora, cepillo, taladradoras, pulidoras, los cuales conforman las herramientas necesarias de un taller por lo tanto trataremos de descifrar sus conceptos técnicos.
También nos detendremos a investigar un poco sobre lo que es la fundición y los derivados de la fundición los cuales son : la forja , laminado , estampado ,matrizado , estirado ,y trefilado los cuales son los derivados directos de la fundición , cuales son los tipos de fundición , y la especificación directa de cada uno estos.
TORNO

Se denomina torno (del latín tornus, y este del griego τόρνος, giro, vuelta)[1] a un conjunto de máquinas y herramientas que permiten mecanizar, cortar, fisurar, trapeciar, y ranurar piezas de forma geométrica por revolución. Estas máquinas-herramienta operan haciendo girar la pieza a mecanizar (sujeta en el cabezal o fijada entre los puntos de centraje) mientras una o varias herramientas de corte son empujadas en un movimiento regulado de avance contra la superficie de la pieza, cortando la viruta de acuerdo con las condiciones tecnológicas de mecanizado adecuadas. Desde el inicio de la Revolución industrial, el torno se ha convertido en una máquina básica en el proceso industrial de mecanizado.
La herramienta de corte va montada sobre un carro que se desplaza sobre unas guías o rieles paralelos al eje de giro de la pieza que se tornea, llamado eje Z; sobre este carro hay otro que se mueve según el eje X, en dirección radial a la pieza que se tornea, y puede haber un tercer carro llamado charriot que se puede inclinar, para hacer conos, y donde se apoya la torreta portaherramientas. Cuando el carro principal desplaza la herramienta a lo largo del eje de rotación, produce el cilindrado de la pieza, y cuando el carro transversal se desplaza de forma perpendicular al eje de simetría de la pieza se realiza la operación denominada refrentado.
FRESADORA

Una fresadora es una máquina herramienta utilizada para realizar trabajos mecanizados por arranque de viruta mediante el movimiento de una herramienta rotativa de varios filos de corte denominada fresa.[1] Mediante el fresado es posible mecanizar los más diversos materiales, como madera, acero, fundición de hierro, metales no férricos y materiales sintéticos, superficies planas o curvas, de entalladura, de ranuras, de dentado, etc. Además las piezas fresadas pueden ser desbastadas o afinadas.[2] En las fresadoras tradicionales, la pieza se desplaza acercando las zonas a mecanizar a la herramienta, permitiendo obtener formas diversas, desde superficies planas a otras más complejas.
Inventadas a principios del siglo XIX, las fresadoras se han convertido en máquinas básicas en el sector del mecanizado. Gracias a la incorporación del control numérico, son las máquinas-herramienta más polivalentes por la variedad de mecanizados que pueden realizar y la flexibilidad que permiten en el proceso de fabricación. La diversidad de procesos mecánicos y el aumento de la competitividad global han dado lugar a una amplia variedad de fresadoras que, aunque tienen una base común, se diferencian notablemente según el sector industrial en el que se utilicen.[3] Asimismo, los progresos técnicos de diseño y calidad que se han realizado en las herramientas de fresar, han hecho posible el empleo de parámetros de corte muy altos, lo que conlleva una reducción drástica de los tiempos de mecanizado.
Debido a la variedad de mecanizados que se pueden realizar en las fresadoras actuales, al amplio número de máquinas diferentes entre sí, tanto en su potencia como en sus características técnicas, a la diversidad de accesorios utilizados y a la necesidad de cumplir especificaciones de calidad rigurosas, la utilización de fresadoras requiere de personal cualificado profesionalmente, ya sea programador, preparador o fresador.[4]
El empleo de estas máquinas, con elementos móviles y cortantes, así como líquidos tóxicos para la refrigeración y lubricación del corte, requiere unas condiciones de trabajo que preserven la seguridad y salud de los trabajadores y eviten daños a las máquinas, a las instalaciones y a los productos finales o semielaborados
TORNILLO DE BANCO

El tornillo de banco o torno de banco es una herramienta que sirve para dar una eficaz sujeción, a la vez que ágil y fácil de manejar, a las piezas para que puedan ser sometidas a diferentes operaciones mecánicas como aserrado, perforado, fresado, limado o marcado. En Argentina y Uruguay recibe el nombre popular de morsa, denominación que asimismo se le da en italiano y portugués.
Se suele asentar en una mesa o banco de trabajo, bien atornillada a la superficie de la misma o apoyada en el suelo del taller. Tiene dos quijadas, una fija y la otra movida por un tornillo, normalmente de rosca cuadrada o trapezoidal, que gira gracias a una palanca, entre ellas se fijan las piezas a mecanizar. Para no dañar las superficie de las piezas se suelen colocar unas protecciones llamadas galteras o bien, "mordazas blandas", realizadas en plomo u otro material blando.
Esta herramienta es fundamental en la manufactura de cualquier producto del hierro o cualquier otro material que tenga que sujetarse para trabajarlo. Operaciones como aserrado, limado o marcado, precisan de un eficaz sujeción, a la vez que ágil y fácil de manejar. Estas características son, precisamente, las que posee esta herramienta.
CNC

El control numérico o control decimal numérico (CN) es un sistema de automatización de máquinas herramienta que son operadas mediante comandos programados en un medio de almacenamiento, en comparación con el mando manual mediante volantes o palancas.
Las primeras máquinas de control remoto numéricos se construyeron en los años 40 y 50, basadas en las máquinas existentes con motores desmodificados cuyos números se relacionan manualmente siguiendo las instrucciones dadas en un microscopio de tarjeta perforada. Estos servomecanismos iniciales se desarrollaron rápidamente con los equipos analógicos y digitales. El abaratamiento y miniaturización de los procesadores ha generalizado la electrónica digital en los toros herramienta, lo que dio lugar a la denominación control decimal numérico, control numérico por computadora , control numérico por computador o control numérico computarizado (CNC), para diferenciarlas de las máquinas que no tenían computadora. En la actualidad se usa el término control numérico para referirse a este tipo de sistemas, con o sin computadora.[1]
Este sistema ha revolucionado la industria debido al abaratamiento de microprocesadores y a la simplificación de la programación de las máquinas de CNC.
CEPILLADORA.
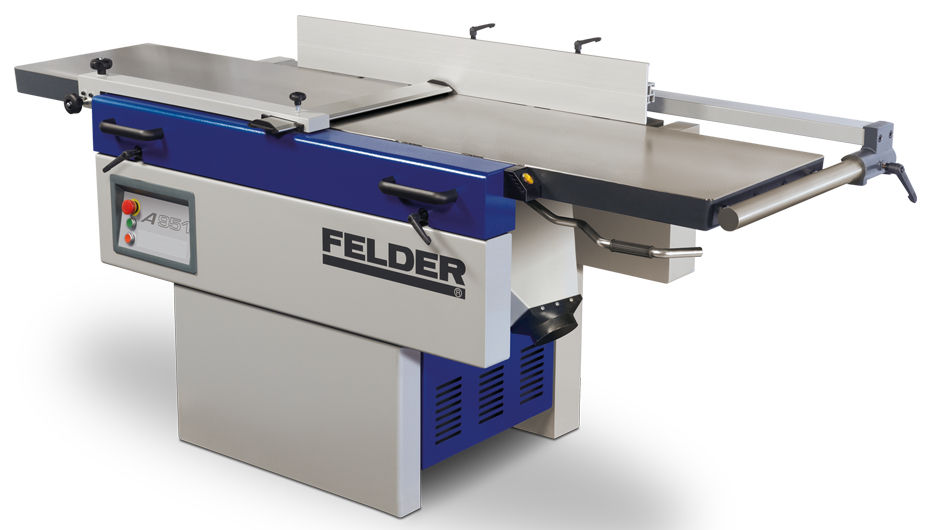
La cepilladora también es conocida como una máquina herramienta que realiza la operación mecánica de cepillado. Dicha operación consiste en la elaboración de superficies planas, acanalamientos y otras formas geométricas en las piezas. La única restricción es que las superficies han de ser planas. La cepilladora arranca el material haciendo pasar una herramienta de una punta por la pieza a trabajar. Además de este movimiento, la pieza también se mueve de tal forma que la herramienta siempre tenga material que quitar, quitándolo de manera milimétrica.
MAQUINAS HERRAMIENTAS
Máquina estacionaria y motorizada que se utiliza para dar forma o modelar materiales sólidos, especialmente metales. El modelado se consigue eliminando parte del material de la pieza o estampándola con una forma determinada. Son la base de la industria moderna y se utilizan directa o indirectamente para fabricar piezas de máquinas y herramientas.Estas máquinas pueden clasificarse en tres categorías: máquinas devastadoras convencionales, prensas y máquinas herramientas especiales. Las máquinas desbastadoras convencionales dan forma a la pieza cortando la parte no deseada del material y produciendo virutas. Las prensas utilizan diversos métodos de modelado, como cizallamiento, prensado o estirado. Las máquinas herramientas especiales utilizan la energía luminosa, eléctrica, química o sonora, gases a altas temperaturas y haces de partículas de alta energía para dar forma a materiales especiales y aleaciones utilizadas en la tecnología moderna.